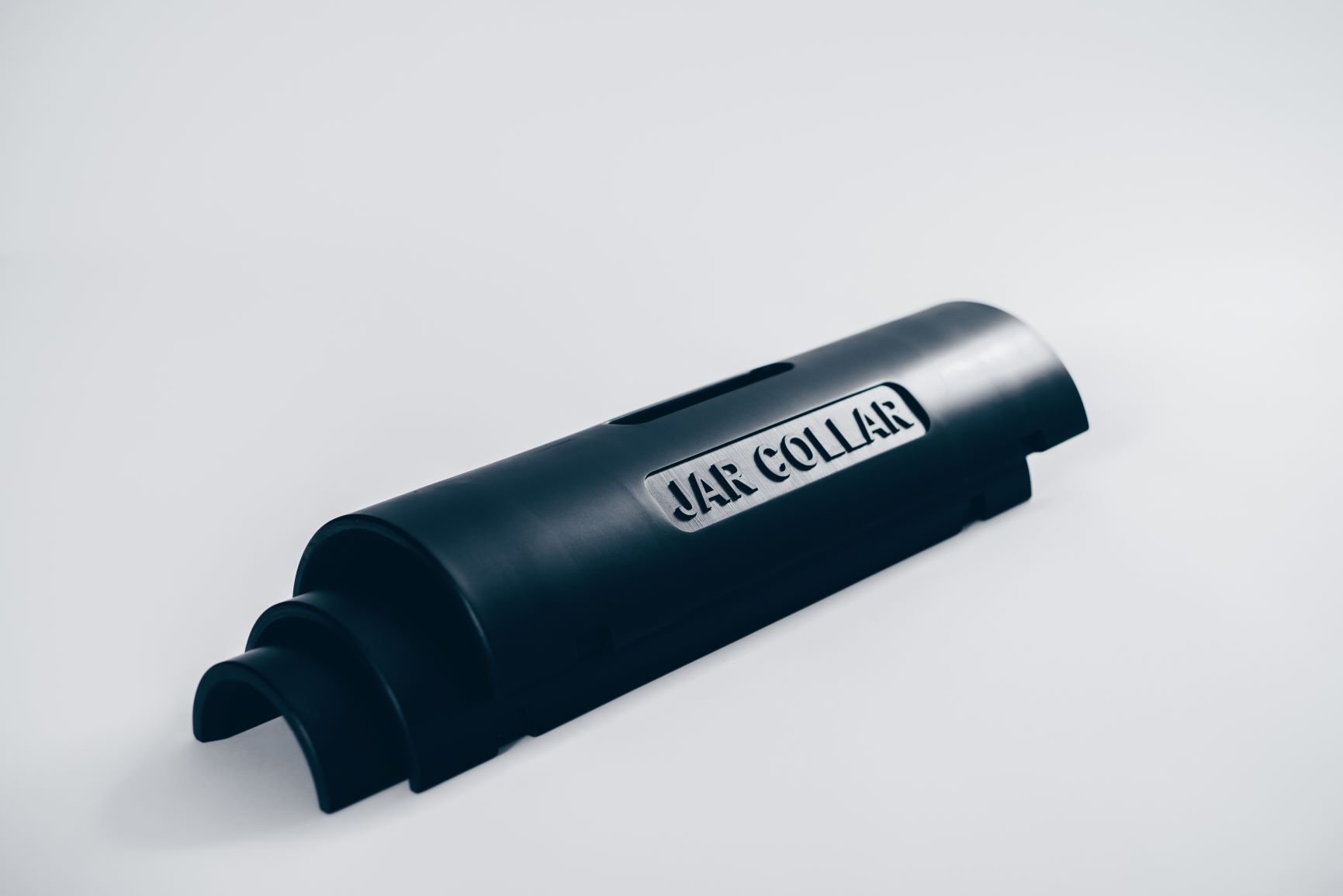
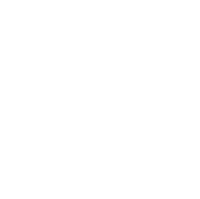
Reaction Injection Moulding
RIM Moulding is used for rapid prototyping and low volume production, as the process offers a fast turnaround and robust end use products.
Tooling alternative | Fast turnaround | Repeatable
What is Reaction Injection Moulding?
Reaction Injection Moulding (RIM) is a manufacturing process used to create lightweight, durable plastic parts by injecting two reactive liquid components into a mould, where they chemically react and cure into a solid shape.
The process involves mixing two low-viscosity liquids—typically a polyol and an isocyanate—which are then injected at low pressure into a closed mould. Inside the mould, the materials chemically react and expand, quickly forming the final part. Once cured, the mould opens, and the part is removed, ready for finishing.
RIM is commonly used for:
- Automotive body panels.
- Housings & enclosures.
Key Benefits of Reaction Injection Moulding
Lightweight, strong parts.
Complex geometries.
Ideal for low to medium production runs.
Smooth surface finish.
Ideal for large, complex parts.
Design flexibility.
Contact us today to get a quote or discuss your part design. Our team of engineers and technicians are ready to help you get the most out of Reaction Injection Moulding.
NDA needed? No problem, download here and email to info@ame-3d.co.uk.
Specifications
Typical reaction injection moulding lead times are 8-10 days; express work available from 3-4 days.
Quantity | Silicone Mould - Up to 50 | Hard Tooling - Up to 1000 |
Tolerances | 0.3mm / 0.3% > 100mm |
Wall Thickness | Min. 3mm (Depending on the overall size. The larger the part, the thicker the wall must be) |
Letters & Logo |
Min. 0.5mm |
Gap between raised & recessed letters |
Min. 0.5mm |
Parts at the end of their lifecycle can be ground into bulk filler for the composite or construction industry.
Materials
If the material you require isn't listed, please contact our sales team.Finishes
- Cosmetic surface finishing
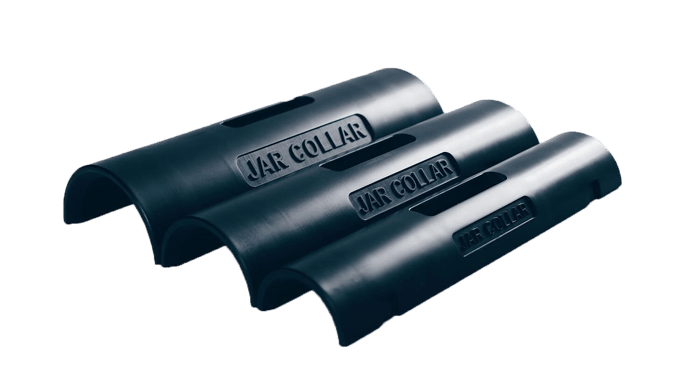
Reaction Injection Moulding FAQs
How does RIM Moulding differ from traditional injection moulding?
Unlike traditional injection moulding, which melts plastic pellets before injecting them into a mould, RIM uses liquid reactants that undergo a chemical reaction to form a solid part. This allows for greater design flexibility, lower tooling costs, and the ability to create large, lightweight parts.
What industries are suitable for RIM applications?
RIM is widely used in industries such as:
- Automotive (bumpers, fenders, interior panels)
- Medical equipment (housings for devices)
- Aerospace (lightweight components)
- Industrial and construction (tool enclosures, protective casings)
How do I optimise my design for reaction injection moulding?
We have created a design guide with specifications for our 3D printing, vacuum casting and reaction injection moulding technologies.
Alternatively, if you require assistance with CAD design, we have our own design department. Send an email to design@ame-3d.co.uk.
Reaction Injection Moulding Quote
Where to find us
+44 (0)1909 550 999
Momentum House, Church Lane, Sheffield, S25 2RG
Monday - Friday | 9AM - 5PM