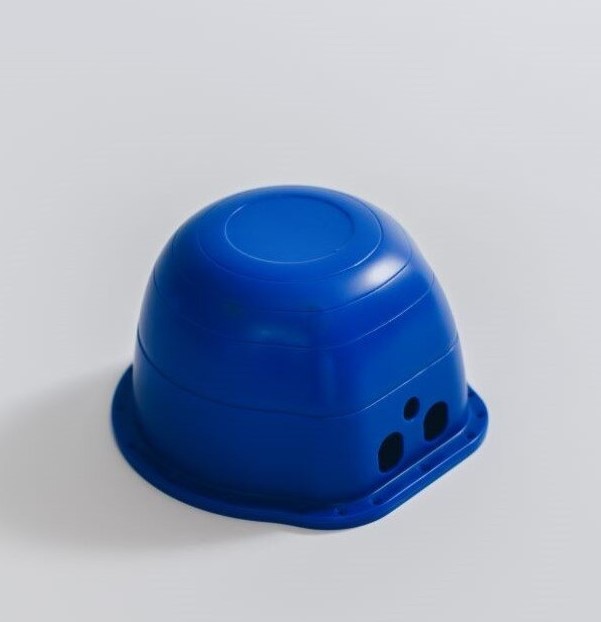
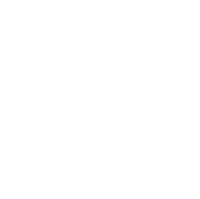
Vacuum Casting
An ideal choice for both rapid prototyping and low volume production of end-use products or parts.
Range of finishing options | High-detailed | Repeatable
What is Vacuum Casting?
Vacuum casting, also known as polyurethane casting, is where an SLA 3D printed part is finished and used as a master & a silicone mould is created from it. This mould is then used to produce multiple copies in resin under vacuum pressure, ensuring bubble-free, high-detail results. It's a go-to method for bridge manufacturing and early product testing. Ideal for producing small to medium quantities of high-quality parts on-demand, similar to injection moulded parts.
An accurate production technique that can replicate detailed patterns, complex dimensions, and different textures. Vacuum casting also is ideal for parts that require overmoulding.
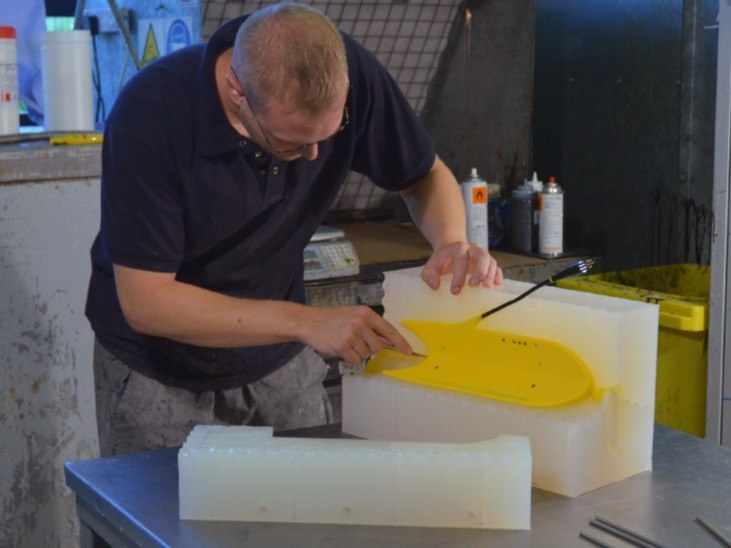
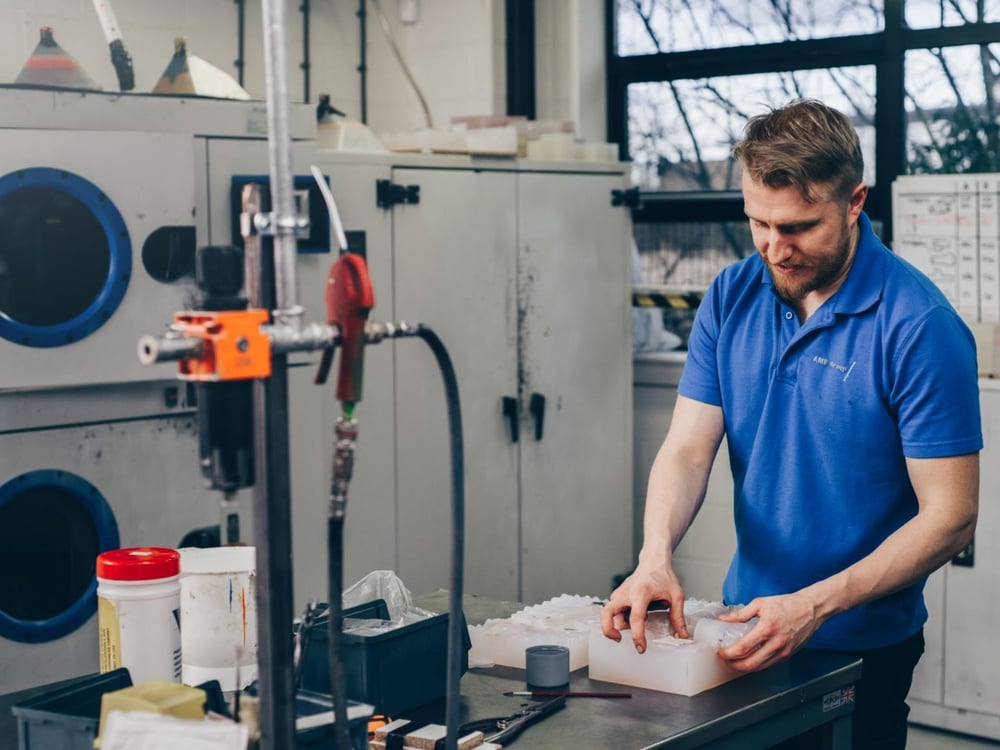
Key Benefits of Vacuum Casting
Smooth surface finish with minimal post-processing.
Fast project turnarounds.
Captures undercuts, fine textures, and detailed features with ease.
Fills the gap between prototyping and full-scale production.
Wide range of polyurethane materials (ABS-like, rubber-like, etc.)
Perfect for producing 10–100 units without the high cost of injection mold tooling.
Contact us today to get a quote or discuss your part design. Our team of engineers and technicians are ready to help you get the most out of vacuum casting—fast, accurate, and cost-effective.
NDA needed? No problem, download here and email to info@ame-3d.co.uk.
Specifications
Typical vacuum casting lead times are 8-10 days; express work available from 3-4 days.
If you require a part longer than 650 mm, please speak to our sales team.
Capacity | 300 x 400 x 350mm | 820 x 600 x 600mm | 820 x 1800 x 600mm | |
Quantity | Up to 20 - 25 parts per tool | |||
Tolerances | 0.3mm / 0.3% > 100mm | |||
Wall Thickness | Min. 1.5 mm (Depending on the overall size. The larger the part, the thicker the wall must be) |
|||
Letters & Logo |
|
0.5mm |
||
Gap between raised & recessed letters |
|
Min. 1.5mm |
Materials
If the vacuum casting material you require isn't listed, please contact our sales team.AME 8891
AME 8891
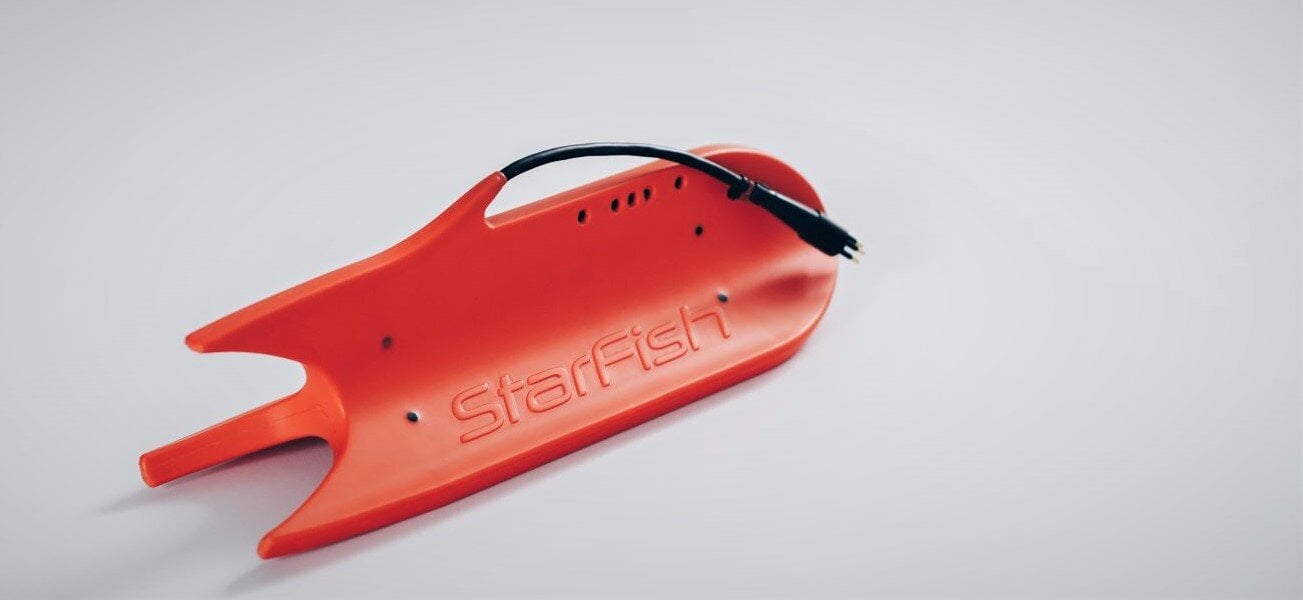
A soft & flexible rubber-like material.
Shore hardness ranges from 20 - 90 A.
AME 8051
AME 8051
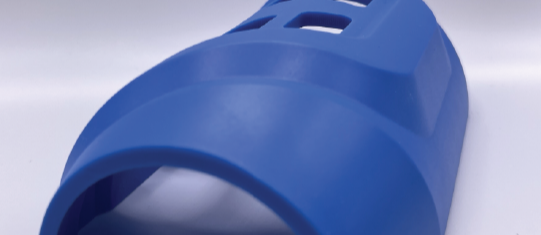
ABS-like material. Ideal for panels and enclosures.
Has a high-temperature resistance.
AME PX234HT
AME PX234HT
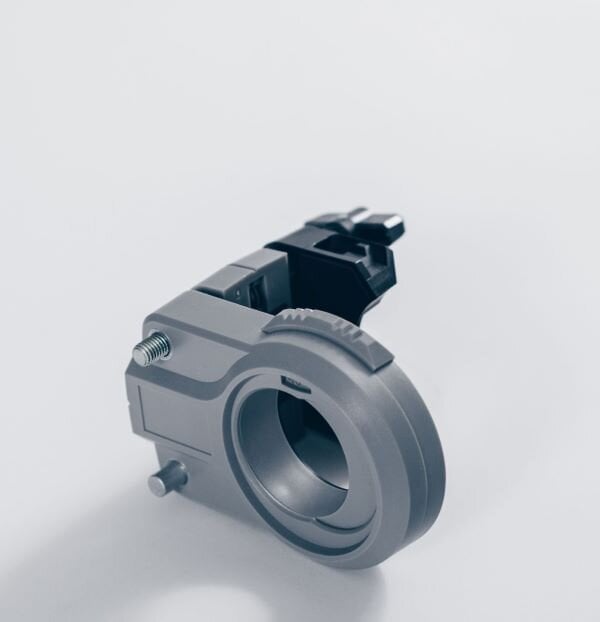
Suitable for prototypes and technical parts.
High-temperature resistance.
AME 3351
AME 3351
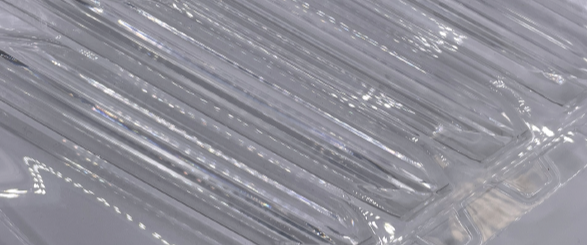
UV-Stable, water clear material. Excellent mechanical properties.
Can simulate thermoplastics.
Vacuum Casting Finishes
- Surface can be specified as textured, matt, satin or gloss.
- Clear or frosted.
- Rubber overmould.
- Matt, satin or gloss metallic finish.
Have a specific visual or functional requirement? We offer specialised finishes upon request to meet branding or technical needs.
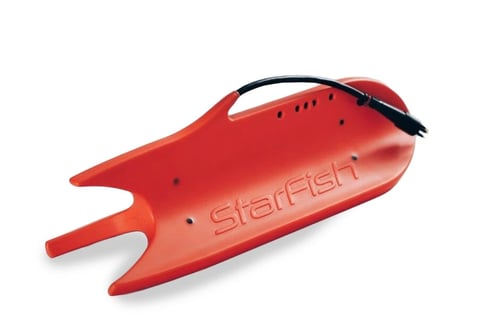
Need manufacturing guidance?
Download our guide to getting cost-effective manufacturing & understanding which process suits your application.
Vacuum Casting FAQs
What are the applications of vacuum casting?
- Prototyping and product testing
- Low-volume production of plastic parts
- Concept models and marketing samples
- Medical device and automotive component development
How does vacuum casting compare to injection moulding?
Vacuum casting is faster and more cost-effective for small runs, while injection moulding is better for mass production. Vacuum casting also allows more flexibility in material selection and design changes.
Can vacuum casting produce coulored or transparent parts?
Yes! Vacuum casting allows for custom colouring, as pigments can be added to the resin. Transparent and translucent parts are also possible using clear polyurethane resins.
How many parts can be made from one silicone mould?
A single silicone mould typically lasts for 20–25 copies before degrading, making vacuum casting ideal for small-batch production.
How long does the vacuum casting process take?
Production time depends on part complexity and quantity, but a typical project can take 7-10 days, including master pattern creation and mould curing.
How do I optimise my design for vacuum casting?
We have created a design guide with specifications for our 3D printing, vacuum casting and reaction injection moulding technologies.
Alternatively, if you require assistance with CAD design, we have our own design department. Send an email to design@ame-3d.co.uk.
Get a Vacuum Casting Quote
Where to find us
+44 (0)1909 550 999
Momentum House, Church Lane, Sheffield, S25 2RG
Monday - Friday | 9AM - 5PM